Inventory Management System: Ultimate Guide for F&B Business
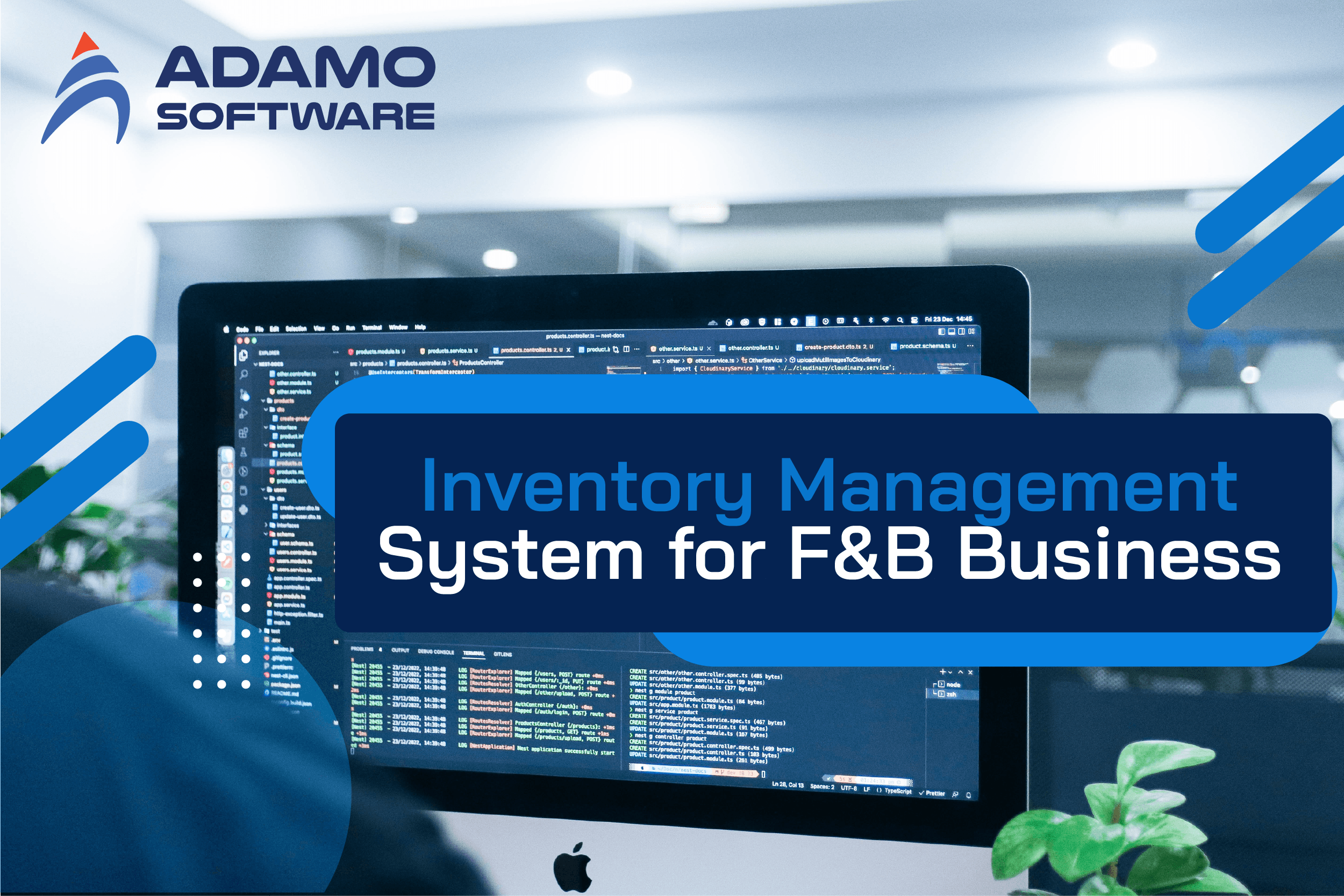
The best inventory management system should help businesses easily track items, tools, and assets from production to sale. Check it out.
An inventory management system is how firms track and control stock before it is sold. Inventory systems, whether automated or manual, strive to reduce inventory carrying costs while ensuring adequate stock is available to fulfill consumer demand.
Here’s a guide to choose one that meets your F&B businesses’ requirements. We look at different types of inventory management systems and how they work, with examples and helpful buying advice. Continue reading to learn more.
I. What is inventory management system?
An inventory management system (or inventory system) is the process of tracking your goods across your whole supply chain, from purchasing to manufacturing to final sales. It regulates how your company approaches inventory management.
If your company keeps a lot of inventory, you must be efficient while maintaining reasonable margins. An efficient inventory management system can assist you in accomplishing this.
In some circumstances, an Excel or Google Sheets spreadsheet will do as an inventory management system for a business. However, many businesses choose dedicated inventory management systems to increase productivity and reduce expenses.
The optimal inventory management system for your unique circumstances depends on factors such as the size, complexity, and inventory requirements of your firm.
II. How does the inventory management system work?
An online inventory management system tracks items along the supply chain by automating the process of changing stock levels and inputting data.
However, it is capable of much more.
An inventory management system can be used to speed up purchasing, create items using a Bill of Materials, fulfill client orders from different sales channels, and expedite dozens of other typical inventory control operations.
You can also read about how a restaurant POS system work in our blog What is restaurant POS system? How to choose the perfect one for your business
III. Different types of inventory management system
1. Automated inventory management system
Stock management software is specifically intended to assist you in tracking and controlling stocks. If the software is cloud-based, you will be able to sync it with your other cloud applications and view your data from any location and at any time.
An automated inventory management system’s goal is to eliminate administration, improve visibility and accuracy, and streamline operational procedures. That means less time and money spent on inventory management and more time spent on sales.
The disadvantage is that automated systems can take time to set up and train on. To ensure a flawless set-up procedure, some firms choose to invest in onboarding packages or implementation partners.
2. Spreadsheet-based inventory management system
Spreadsheet-based inventory management systems (using an Excel or Google Sheets doc to track inventory) can be a wonderful approach to managing inventory on a small scale.
However, spreadsheet inventory systems have a few drawbacks.
For example, when utilizing spreadsheets, human errors can quickly snowball into costly difficulties. Furthermore, flexibility and accuracy might be difficult to come by.
However, if the spreadsheet fails, your inventory management system fails as well. They necessitate a significant amount of manual input and analysis. And when your company grows in complexity, it will become unwieldy.
3. Basic stock management system
Some cloud-based business tools, such as accounting software, have basic inventory management capabilities.
While not as thorough as a dedicated inventory management system, it is frequently the next step up from spreadsheets. These systems often allow you to link inventory tracking to the process that the app was designed to optimize.
Unfortunately, basic inventory management systems sometimes lack the most critical capabilities required by medium or sophisticated business types.
4. Asset inventory management system
An asset inventory management system is a tool that assists firms in managing the resources on which they rely. Most of the time, those resources are physical things like tools, machinery, and corporate vehicles. Asset inventory management, on the other hand, might include digital assets and intellectual property.
While traditional inventory management systems focus on inventory associated with products sold, asset inventory management technologies focus on inventory required to run the firm.
Asset inventory tracking systems are available. However, it is also possible to manage asset inventory using standard inventory management software or a spreadsheet-based method.
5. Accounting and inventory management system
An accounting and inventory management system might consist of a single piece of software or two or more integrated cloud-based systems that allow a company to synchronize inventory management with financial reporting.
The key advantage of linking your accounting and inventory management systems is that it promotes accuracy and uniformity throughout the organization. Both systems automatically record stock movements, improving visibility into business costs and the company’s present value.
6. 3PL inventory management system
A third-party logistics (3PL) inventory management system is a software application that assists 3PL organizations in tracking and managing all products entering and exiting their fulfillment centers.
Because 3PL suppliers frequently interact with several clients with varying needs, a robust inventory management system is frequently required.
7. ERP inventory management system
An ERP inventory management system is a single solution that covers all aspects of business planning, as opposed to many cloud components that interface smoothly with one another.
There are numerous advantages and disadvantages of using an ERP system over specialist inventory software.
One significant advantage is that you only need to learn one system and deal with a single software vendor. You can receive a unified solution that may encompass inventory, accounting, supply chain, human resources, and other areas.
8. Cloud-based inventory management system
A cloud-based inventory management system, often known as cloud-based inventory software, is a computerized system that uses the Internet to record stock levels and inventory data. This allows firms to remotely track inventory and combine it with other cloud software systems.
Cloud inventory systems enhance order administration and save inventory expenses by eliminating the need for human stock checks and other administrative duties.
9. Warehouse management system
A warehouse management system (WMS) assists businesses in organizing, managing, and optimizing their storage facilities.
Warehouse management is the process of empowering your warehouse crew to work as efficiently as possible. Typically, the software includes features for streamlining the management of items within a warehouse.
A WMS can help with inventory control. However, it is not the same as an inventory management system. WMS solutions frequently lack important inventory management system functions such as purchasing, production, and stock control.
10. Barcode inventory management system
A barcode inventory management system is used to assign a number to each product sold by a company. Multiple data points, such as the supplier and product dimensions and weight, can be associated with the barcode number. The barcodes can also track changeable data, such as how much of a product is in stock.
All big merchants utilize barcodes in their inventory management systems. When a barcode is read in a retail environment, the information on inventory sales is immediately read in a more sophisticated database that maintains the usage of statistics. It uses sales data to make purchasing decisions based on sales and inventory levels.
IV. What should a good restaurant inventory management system do?
1. Accurate forecasting
Accurate demand forecasting is the first step in a good inventory management system. Businesses can forecast future demand and plan inventory levels by examining previous sales data, seasonal trends, and market circumstances. This can be accomplished using numerous techniques such as moving averages, weighted averages, and advanced statistical models. Accurate forecasting helps organizations avoid stockouts and overstocking.
2. Set reorder points and safety stock levels
Businesses must create reorder points and safety stock levels to avoid stockouts. The inventory level at which a fresh order should be made to refill stock in time is known as the reorder point. It is independent of parameters such as lead time, demand variability, and desired service level. A safety stock is an extra quantity of stock stored to absorb unforeseen variations in demand or supply disruptions.
Businesses may maintain a smooth flow of goods and reduce the risk of stockouts by establishing suitable reorder points and safety stock levels.
3. Utilize technology and automation
Technology is critical to good inventory management. Inventory management systems can assist organizations in tracking stock levels, tracking sales patterns, and producing accurate reports. This software can automate operations like order placement, demand forecasting, and inventory management, decreasing human error and saving time.
Furthermore, technologies such as barcode scanners, RFID (Radio Frequency Identification), and IoT sensors provide real-time inventory visibility, expediting operations and boosting inventory accuracy.
Explore some setting new rules for the food delivery industry in a post-pandemic.
4. Categorize inventory
It is critical to categorize inventory depending on its nature and turnover rate. ABC analysis is a prominent classification method that splits inventory into three categories: A, B, and C. High-value commodities with limited demand variability, such as expensive wines or specialty ingredients, fall into Category A, goods in Category B have moderate value and demand variability, but goods in Category C have low value and high demand variability, such as disposable cutlery.
Businesses can prioritize their inventory management efforts and spend resources accordingly by categorizing inventory.
5. Establish strong supplier relationships
Strong supplier relationships are essential for good inventory management. Regular communication, on-time payments, and negotiating advantageous terms can all assist firms in securing dependable and efficient supply chains.
Collaboration with suppliers can also result in greater market insights, improved delivery schedules, and even cost savings through bulk purchasing or discounts. Strong supplier relationships can assist firms in maintaining ideal inventory levels and rapidly responding to changes in demand.
6. Implement a just-in-time (JIT) inventory management system
Just-in-time inventory management is a lean method that tries to reduce inventory levels while maintaining product availability. Businesses can cut holding costs, minimize waste, and increase cash flow by getting goods from suppliers just in time for manufacturing or sale. However, implementing JIT necessitates effective supplier coordination, dependable delivery schedules, and solid quality control methods.
While JIT might be difficult to implement in the F&B business due to perishable products, it can be done with non-perishable commodities or with careful coordination with suppliers and production processes.
7. Utilize the First-In, First-out (FIFO) method
Adopting the FIFO strategy is critical in the F&B industry, where product freshness is critical. Older products are sold or used first. Consequently, it lowers the risk of spoiling or obsolescence. Implementing correct labeling and storage procedures can assist organizations in identifying the oldest products and keeping them fresh. FIFO not only reduces waste but also increases consumer satisfaction by providing them with new and high-quality products.
8. Conduct regular inventory audits
Regular inventory audits are required to ensure accuracy and identify any irregularities. Audits entail physically counting the inventory on hand and comparing it to the system records. This aids in the detection of issues such as theft, misplacement, or data entry errors. Regular audits also allow businesses to detect slow-moving or obsolete commodities and take necessary action, such as discounting or liquidation, to free up money and avoid excess inventory development.
9. Monitor key performance indicators (KPIs)
Tracking KPIs is critical for assessing the effectiveness of inventory management activities. Inventory turnover ratio, gross margin returns on inventory investment (GMROI), and stockout rate are all key performance indicators. Businesses may discover areas for improvement, quality the impact of inventory management initiatives, and make data-driven decisions to maximize inventory levels and profitability by constantly monitoring these KPIs.
10. Continuous improvement and adaption
An inventory management system is a continuous process that necessitates constant improvement and response to changing market conditions. It is critical to analyze and alter inventory plans regularly depending on consumer input, market trends, and internal performance data. Businesses must keep up to date with new technology, industry best practices, and regular changes that may affect inventory management procedures.
Businesses may maintain a competitive edge in the F&B industry by being proactive and adaptable in their inventory management system.
V. Comparing: Periodic vs perpetual inventory systems
Periodic inventory | Perpetual inventory |
Periodic inventory is a method of stock management that is fully based on stock taking. Businesses that use a periodic approach count their stock on a regular basis — say, every 3 to 6 months — to ensure stock accuracy and to see if stock levels match sales data. | Perpetual inventory is a system that tracks stock levels while items are received, manufactured, sold, or returned to the business. Continuous inventory systems typically provide the most up-to-date inventory figures, with less reliance on stock takes for accuracy. |
VI. How much does this inventory management system cost?
Inventory management systems can cost anything from nothing to thousands of dollars per month in monthly fees. We discovered that the average inventory management system costs USD 175 per user license per month after researching over 70 software suppliers listed on the software review site Capterra.
Users of cloud-based inventory systems should also expect to pay roughly USD 80 per month for continuing customer assistance and an average of USD 789 for one-time setup fees.
Implementation fees for major organizations wishing to invest in multi-faceted ERP inventory solutions can range from USD 10,000 to 40,000. There are also the expenses of business disruption during adoption to consider.
VII. How to build an inventory management system
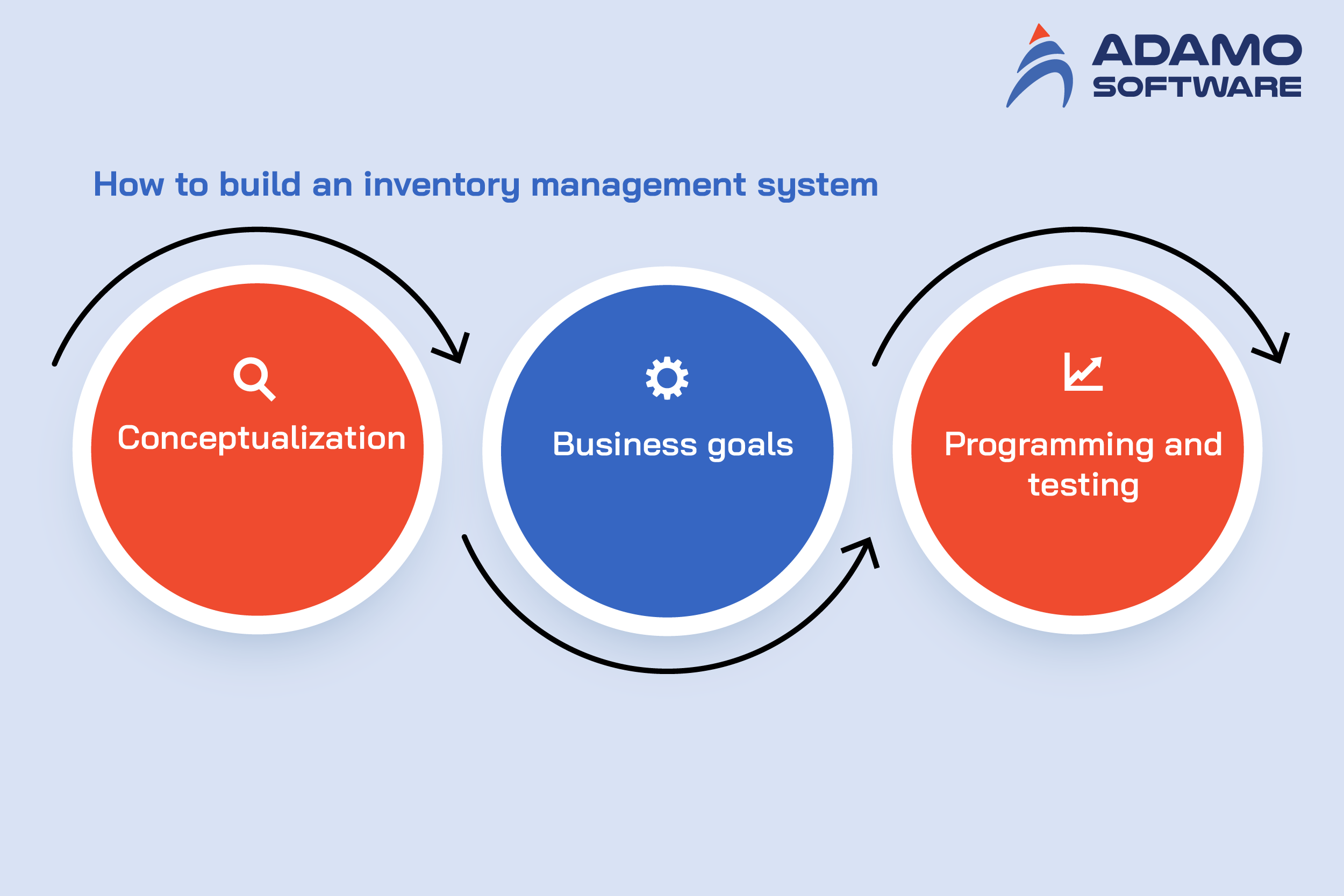
Step 1. Conceptualization
Begin by examining what your company does daily and identifying the functional areas that are involved and can be easily tracked using data. Then, look at other companies in your field that have utilized similar software and how they have used it to boost productivity. Determine which of your operations could benefit from automation. It is critical to understand what you require before designing the ideal answer to your difficulties.
Step 2: Business goals
Do you want to create an inventory management system to help you swiftly store and deliver fresh products to clients, or do you intend to use an IMS as part of a larger eCommerce strategy? Your major objective and company goals should be clearly defined at the start of the process. Clarify the specific use cases and work to meet the expectations.
Step 3: Programming and testing
Typically, once you’ve specified your software requirements, it’s time for engineers to build code, which includes code for the program itself as well as any supporting tools and libraries. Engineers must test their developed code in addition to writing it to ensure that any bugs or flaws are fixed before implementing it.
This phase often entails numerous iterations and several changes to current functionality for the software to perform as intended and be enhanced further by other developers. Documenting the design process for software is also a crucial aspect of maintaining and improving its quality. Following the development of inventory management software, the next steps are implementation and maintenance.
VIII. Why select Adamo to build your food inventory management system
As a leading food and beverage software development company in Vietnam, Adamo Software provides many food and beverage software solutions from restaurant CRM system, inventory management system, and more. Besides, in every project, Adamo always focuses on the time to launch the project promptly and easily in the market, the ability to allocate human resources when needed, and the offering of lucrative software solutions related to the food and beverage industry.
F.A.Q
1. What are the features of the inventory management system?
When selecting an inventory management system, key features to consider include:
– Inventory management.
– Automation and notifications for stock alerts.
– Order administration.
– Scan barcodes.
2. List examples of the inventory management system
2.1. A small business using a spreadsheet system
Consider the following example of a small business inventory management system:
Tom and Mary own and operate a food hamper business. They have several suppliers from whom they buy food and ingredients in bulk, some of which must be separated and packed.
Tom makes an Excel spreadsheet that he updates anytime he orders more items or puts together a hamper. Mary runs the shop, so whenever a sale occurs, she updates the spreadsheet. This is their inventory control system.
Tom and Mary rely exclusively on the spreadsheet to determine how much inventory they currently have, when their food products may expire, and when to reorder more ingredients.
2.2. A global enterprise using a cloud-based system
ToyFun Inc. Creates toys for children. They offer them in bulk to shops all around the world. They also offer direct-to-consumer (D2C) through various web channels.
ToyFun manufactures and sells so many toys that they require three distinct warehouses to store them all. They employ a cloud-based inventory management system solution to keep track of all their goods because they have so many parts and products to manage.
The software allows them to view how many stocked items they have in each of their warehouses. It seamlessly syncs online sales with their recorded inventory, ensuring that stock levels are always correct.
To provide inventory reports based on past sales data, ToyFun also employs an online inventory system. This assists them in forecasting future sales demand. Based on historical lead times, they can even estimate the dependability of their suppliers.
As a result, ToyFun may make more informed purchase decisions that protect cash flow and promote growth.
3. Why do I need an inventory management system?
A good inventory management system is needed for:
– Keeping appropriate inventory levels.
– Avoiding stockouts and overstocking.
– Enhancing order fulfillment.
– Improving supply chain management operations.
– Improving total efficiency.
It allows you to make more informed decisions based on real-time inventory data, which improves customer satisfaction.
4. Which type of inventory management system fits best for your business?
The best inventory management system is determined by a variety of factors, including the size of your firm, industry-specific requirements, sales volumes, and supply chain complexity.
To identify the best solution for your circumstances, you must first examine your business demands and speak with experts or software vendors.