What is Supply Chain Management System (SCM)?
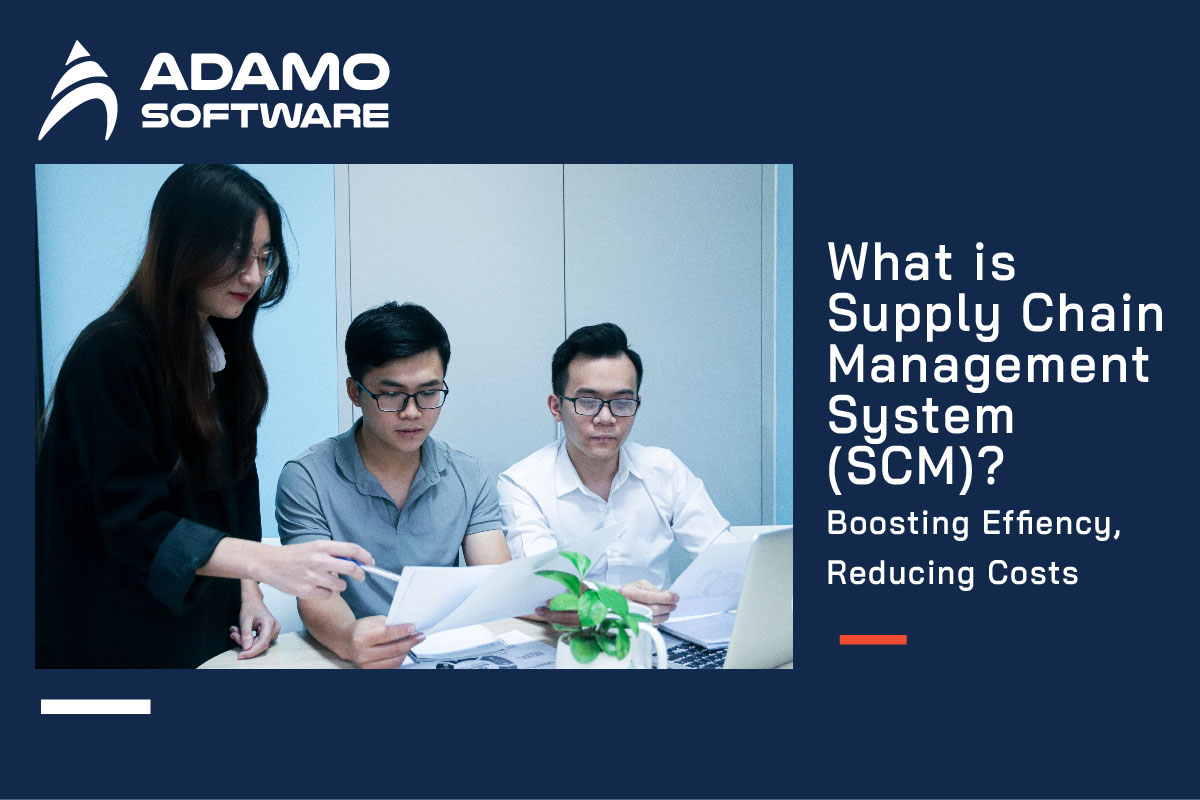
This article will go over everything about supply chain management system. By utilizing automation, business profitability can be boosted.
Supply chain management (SCM), a complex network in the current global economy, is responsible for the planning and control of the transfer of products and services from suppliers to customers. To compete in this industry, you must be willing to consistently keep up with the market.
Companies must use supply chain management systems to optimize their supply networks, cut costs, and improve customer satisfaction. Without it, businesses may struggle to fulfill today’s market demands and remain competitive.
I. What is a supply chain management system? SCM system definition
A supply chain management system (SCM) is a multi-organizational solution that oversees the transformation of raw materials into completed goods.
While numerous types of supply chain management systems specialize in various areas, there are also complete supply chain management systems. These SCM systems help businesses by managing several supply chain processes, including:
– Procurement
– Planning
– Product or service creation
– Order completion
– Order administration
These functions shouldn’t be segregated within the organization. Rather, the SCM platform must be accessible throughout the supply chain, including all stakeholders, such as:
– Suppliers
– Manufacturers
– Wholesalers
– Transportation providers
– Logistics managers
– Retailers
This ensures that everyone can see the product or service as it travels through the manufacturing process.
Companies that acquire more control over these processes can speed up delivery, improve the customer experience, and reduce supply chain costs.
II. How supply chain management works
A supply chain management system is a continuous endeavor by businesses to make their supply chains as efficient and cost-effective as feasible.
Typically, SCM aims to centrally control or link a product’s manufacturing, shipment, and distribution. Companies can reduce superfluous expenses and unnecessary stages in the supply chain, allowing them to deliver items to customers faster. This is done by maintaining tighter control over internal inventories, internal manufacturing, distribution, sales, and vendor stocks.
The supply chain management system is founded on the premise that practically every product that enters the market is the result of the efforts of numerous enterprises that comprise a supply chain. Although supply chains have existed for centuries, most businesses have only recently recognized them as a value-add to their operations.
III. Components of a SCM system: 5 phases
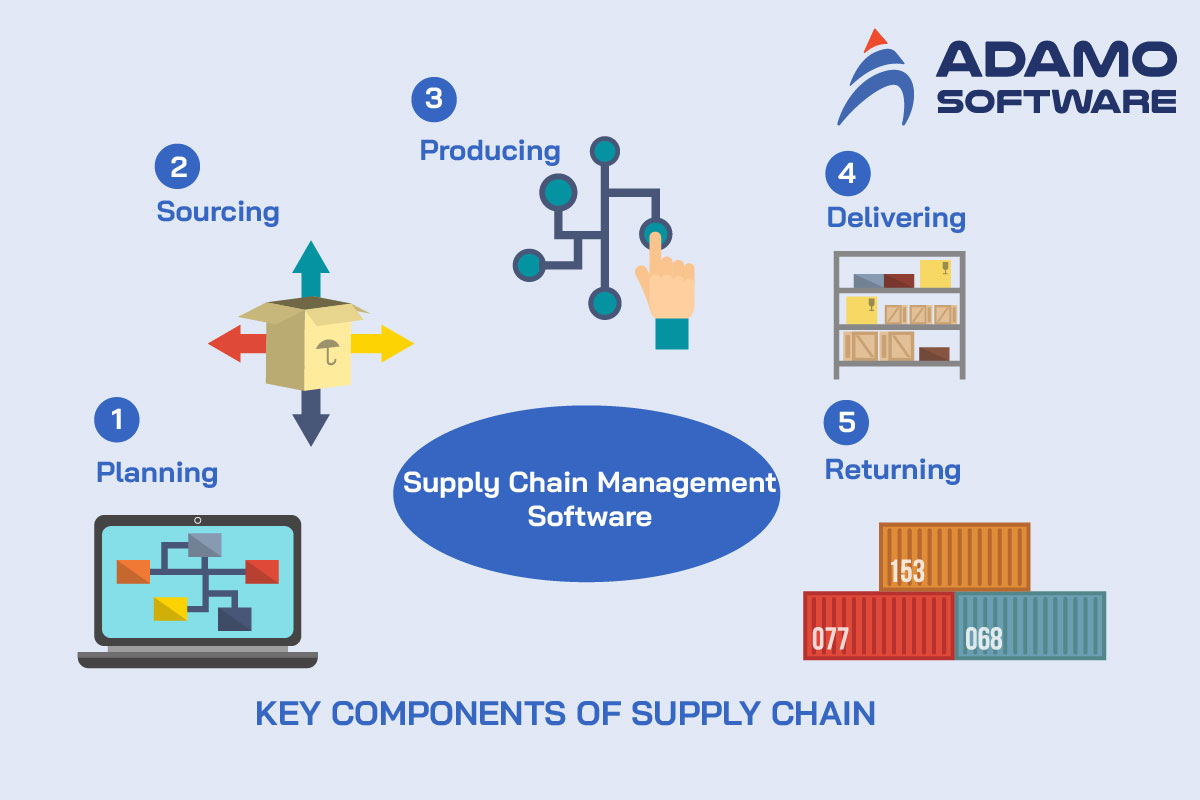
1. Planning
Companies must plan and manage all resources effectively to meet client demand for their products or services. This can be accomplished by carefully choosing the technology to utilize, ensuring that the supply chain remains efficient and effective.
2. Sourcing
Every firm must choose a supplier or multiple suppliers to provide the commodities and services required to manufacture their products. Following the selection of vendors, the supply chain management system must monitor and manage supplier relationships. Ordering, receiving, controlling inventory, and authorizing supplier payments are all part of the job.
3. Producing
The supply chain management system must organize the actions required to order raw materials, accept them, make them into finished products, test items for quality, package products for shipping, and plan each shipment for delivery.
4. Delivering
Logistics and supply chain management are closely related. The delivery process includes coordinating orders, picking, packing, scheduling deliveries, invoicing, dispatching, alerting appropriate parties, and receiving payments. Even with third-party courier services in place, every single transaction must be closely monitored to ensure no errors occur, as a single inaccuracy might create a considerable delay.
5. Returning
Businesses must design a method for returning products as part of their supply chain management. This comprises a procedure for handling client returns and assessing whether the product should be replicated, repaired, discarded, or restocked.
IV. Different types of supply chain models
1. Continuous flow model
This model, one of the more classic supply chain strategies, is frequently suitable for mature industries. The continuous flow concept is based on a company manufacturing the same good repeatedly and expecting little variation in consumer demand.
2. Agile model
This concept is ideal for businesses with erratic demand or custom-order products. This approach emphasizes flexibility because a firm may have a special requirement at any time and must be prepared to pivot accordingly.
3. Fast model
This approach highlights a product’s quick turnover and short life cycle. A corporation uses a rapid chain model to capitalize on a trend, swiftly make goods, and ensure the product is entirely sold before the trend ends.
4. Flexible model
The flexible model works best for organizations that are subject to seasonality. During peak season, certain businesses may have substantially higher demand requirements. At the same time, others may have minimal volume requirements. A flexible supply chain management paradigm means that output may be rapidly ramped up or scaled down.
5. Efficient model
Companies operating in industries with extremely low-profit margins may seek to gain an advantage by making their supply chain management process the most efficient. This includes making the most use of equipment and machinery, as well as managing inventories and processing orders as effectively as possible.
6. Custom model
If none of the preceding models meet a company’s requirements, it can always turn toward a custom model. This is common in highly specialized businesses with high technical requirements, such as vehicle manufacturing.
V. Supply chain management system benefits
1. Increased Agility
Customers want to be able to choose their checkout options, shipping timelines, pickup locations, and other details. In turn, customers will reward brands that can meet these objectives with repeat purchases and lasting loyalty.
A strict supply chain management system unable to conform to these expectations will fail to keep up.
Prioritizing fluidity can also help businesses navigate around challenges that threaten to stall production, such as sourcing or regulatory compliance issues. The capacity to change parameters as needed is critical, and newer supply chain management systems offer this benefit.
2. Cloud connectivity
The daily variations of the modern supply chain might make on-premises outdated systems impossible to adjust. For example, if a sourcing problem arises unexpectedly, a custom-coded application may be unable to change parameters and adjust properly.
However, a cloud-based system can take advantage of Industry 4.0 technology to enable rapid adjustments.
Instead of full-scale cloud migration, many businesses are embracing supply chain management systems that allow them to exploit their existing assets while including some parts of cloud-based SCM.
3. Meeting demands for trust and traceability
It has always been critical for businesses to have real-time access to their supply chain. However, rising customer expectations and shifting legal constraints have elevated traceability from a desirable feature to a need.
An intelligent supply chain management system incorporates traceability features into the SCM process.
While this current supply chain management system can assist all businesses, it is especially vital in highly regulated areas such as the F&B sector. F&B businesses are positioning themselves to satisfy client demands, reduce product lifecycles, and remain agile amid market fluctuations by using these technologies.
VI. Identify the weaknesses of supply chain management systems
1. Cost
Implementing supply chain management systems can be costly, especially for SME businesses. This can be a substantial barrier to adoption, and some businesses may find it difficult to justify the expense of investing in a supply chain management system.
2. Complexity
Supply chain management systems can be complex, and firms may need time to learn how to use them efficiently. This might lead to a steep learning curve, which can be difficult for some businesses.
3. Integration
Integration of supply chain management systems with other business systems, such as ERP and CRM systems, is required. This can be a complicated procedure, and it may take some time to guarantee that all the systems are communicating efficiently.
4. Maintenance
Supply chain management systems require regular maintenance and updates to guarantee that they continue to perform properly. This can be time-consuming and costly. Therefore, some firms may struggle to keep up with the supply chain management system’s maintenance requirements.
VII. How much does a SCM system cost?
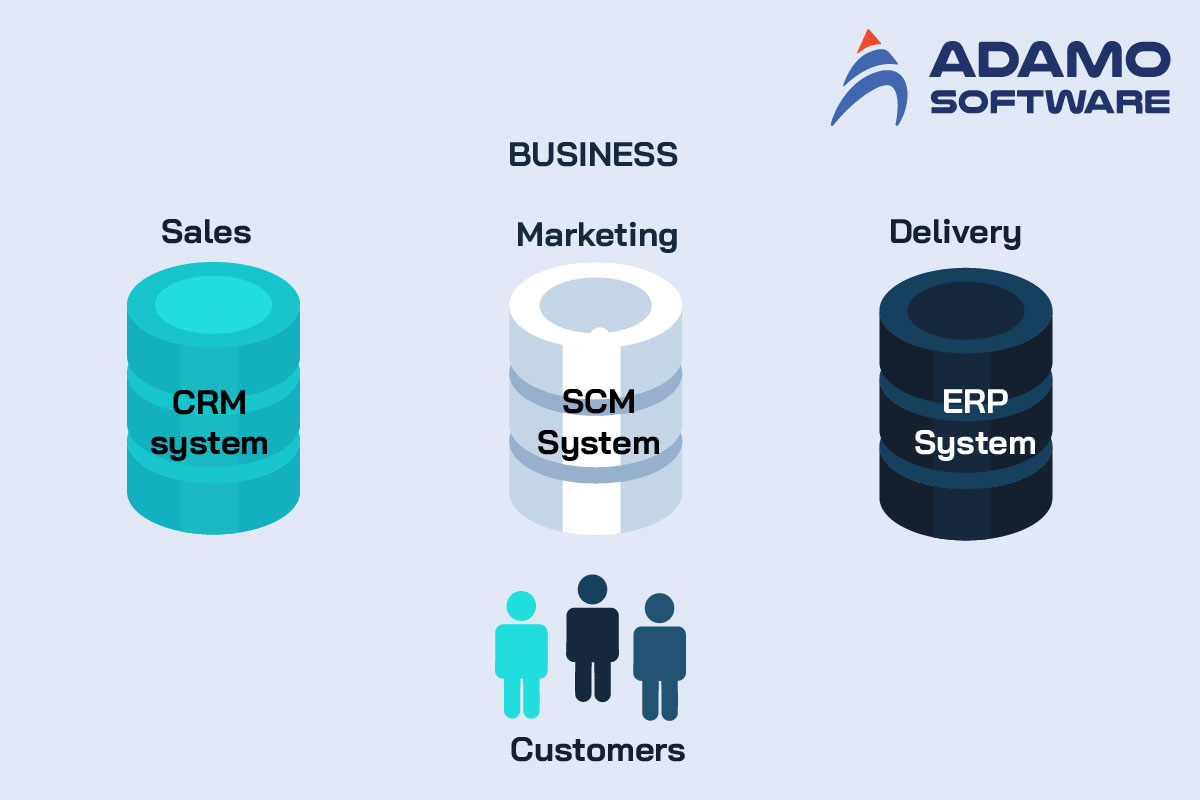
The cost of developing the supply chain management system is affected by the level of functionality offered in the software. Large enterprises with several departments should choose a full ERP solution. A fully functional software solution will be more expensive. The following elements also influence the final cost of custom software development:
– Number of users
– Hourly software development costs
– Infrastructure
– Ongoing support and maintenance
Supply chain management system creation is quite affordable, and the user can create it in a matter of minutes. The costs of developing the supply chain management system will range from $15,000 and $40,000. If you need an automated solution for your organization’s operations, you can hire a firm to determine the actual cost of developing a supply chain management system.
VIII. How are ERP, SCM, and CRM systems related to each other?
Combining an ERP and SCM system can assist manufacturers in various ways, including:
Explore common types of business software: ERP vs CRM vs SCM.
– Improved inventory planning and management.
– Allowing procurement to make better purchase and supplier selection decisions.
– More efficient management of complicated supply chain networks.
An ERP system focuses on business administration to improve efficiency in areas such as purchasing, inventory, delivery, and billing. And, owing to connectivity with an SCM system, the entire receiving and manufacturing processes will be visible to an ERP solution.
CRM is the opposite of SCM. However, an ERP and CRM system unifies data relating to customer interactions. Other sections of the organization can obtain this essential information by connecting customer data with an ERP.
SCM is concerned with the management of supplier relationships. CRM stands for customer relationship management. ERP is concerned with the management of operations and business.
When they work together, all the organization’s data is available once during the first transaction, retained centrally, and updated in real-time. This combination produces a very effective tool for all corporate management.
Read more about CRM system in our dedicated article What makes Restaurant CRM System the “secret weapon” of restaurant
IX. Today’s supply chain management: Industry 4.0 & SCM
1. Improved maintenance functions
The way businesses use technology to supply chains in Industry 4.0 is radically different from how they have done it in the past. For example, in the maintenance role, firms would often wait until a machine broke down before repairing it. Smart technology has altered this. We can now detect failure before it occurs and take preventative measures to keep the supply chain running smoothly.
Supply chain management system nowadays is about leveraging technology to make the supply chain and the organization smarter.
2. Meet customer needs and financial goals
Industry 4.0 SCM also has a big benefit over traditional SCM in that it enables synchronized planning and execution while also offering significant cost savings. Companies that use a “plan-to-produce” methodology, for example, must establish an accurate prediction. This entails juggling a slew of inputs to ensure that what is produced meets market demand without exceeding it, hence avoiding costly overstocks.
Intelligent supply chain management systems can assist you in meeting both client demand and financial goals.
3. Help employees contribute more value to the business
An intelligent supply chain management system has additional benefits. For example, it can free up supply chain employees to contribute to the business in more valuable ways. Better supply chain management systems that automate routine processes can provide supply chain professionals with the tools they need to successfully deliver the products and services for which the supply chain is created.
X. Why Should Work with Adamo to Build Your Supply Chain Management System
As a prominent software development company in Vietnam, Adamo Software is an ideal company helping you to build efficient and lucrative CRM and POS restaurant systems. We bring exceptional ideas into your business by adding features and optimal solutions. Besides, at Adamo, we focus on the three things including shortening the time to the market launch, offering a cost-effective solution and supporting allocating human resources in every project. If you are looking for an IT hub for your restaurant operation, Adamo can be a perfect choice for many reasons. Contact us if you have any questions so far.